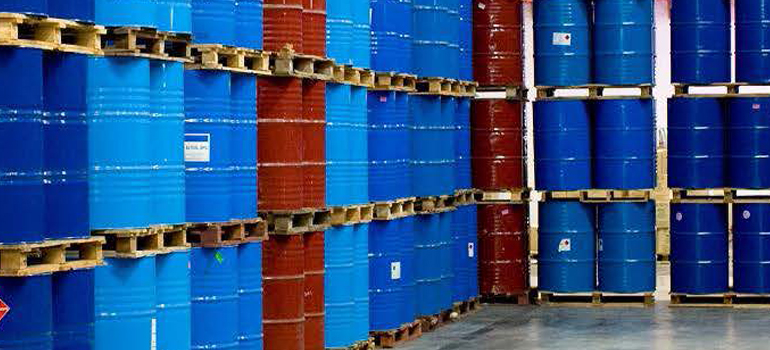
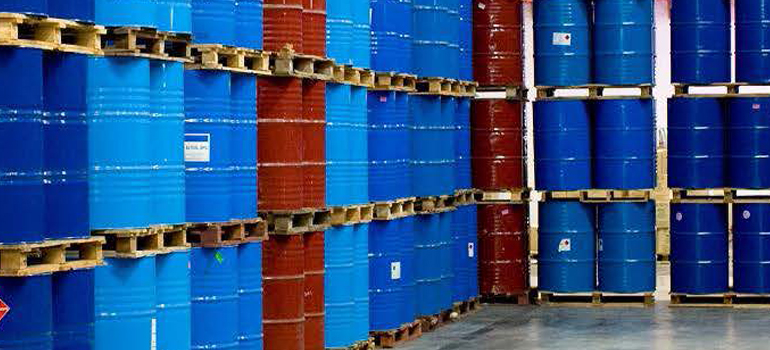
Chemicals Not in Your Line of Sight?
RFID Gives You a Clear View
There are known issues within laboratories that involve tracking, inventorying and accounting for compounds, chemicals and reagents. If this issue has ever presented itself in your laboratory, radio frequency identification (RFID) solutions will help you and your staff monitor every chemical that enters and exits your facility.
Even if you are already using barcode technology, there are numerous benefits that RFID offers over barcode. For example,
- RFID can read multiple tags at once, instead of just one tag at a time like barcode.
- RFID labels can be read at a distance and without line of sight, instead of having to point the scanner directly at the label like you have to for barcode.
- RFID is even more efficient than barcode. In the latest inventory time test, RFID tags allowed the tester to read 48 bottle tags in just 4.2 seconds. To scan the same 48 bottles with barcoded labels, it would take 2 minutes and 31 seconds. The pen and paper inventory method took 9 minutes and 4 seconds to count and record the same 48 bottles. Click here to watch the video of this test.
Overview:
A large pharmaceutical company was looking to track all of their chemicals and reagents (from now on referred to by the generic term ‘chemicals’) when received, when consumed and when they were disposed.
Initial on-site analysis and testing was done to determine the best technology for the read points, product containers and lids. After the analysis, it was determined that the current barcode label would be used and RFID technology would be integrated into their existing system in the receiving area. RFID technology would then be utilized for both inventory and chemical disposal. Following the on-site visit, testing was conducted to determine the best class RFID tag frequency, size and appropriate hardware for the project
Integration/Solution:
Receiving
A hybrid RFID/Barcode initialization station was integrated in the receiving area. This station utilized the client’s existing software along with the RFID integrator’s software. This created the association between chemicals and the RFID tags for inventory reconciliation. As new items were processed into the facility, the operators performed their current check-in sequence, and created the barcode label.
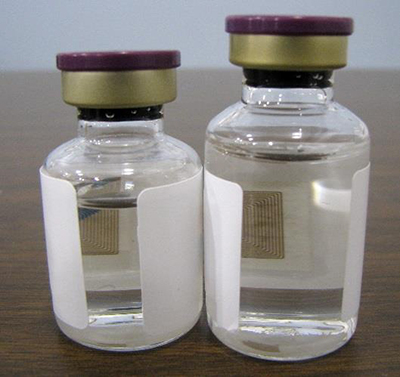
Example of RFID enabled label
The RFID enabled label was attached to the container or lid. The RFID/barcode initialization station then detected the presence of an item, scanned the barcode, and ensured that the barcode was in the correct format to be written to the RFID tag.
The software program then verified that the correct barcode ID had been written to the RFID tag. This transaction was displayed on the RFID/barcode station screen and confirmed by the viewable light stack and audible signal.
Inventory
Inventory was conducted using an RFID enabled wireless/battery powered mobile cart. The cart was used in thestorage rooms. Due to size constraints, an RFID enabled handheld reader was also used to take inventory of chemicals that were in storage or in use.
The process of conducting an inventory became much less time consuming as well as increased the accuracy to over 99.8%. All of the data gathered during each inventory was filtered through the integrator’s software and was automatically reconciled with the pharmaceutical company’s software system. This process made reconciling inventory issues a quick and painless process.
Shelf Life
The RFID system also allowed the employees to know when a chemical’s shelf life had expired or was about to expire. With the chemical’s expiration information stored directly in the RFID tag, the employees could use a handheld reader (or a fixed reader) to pull the expiration information. If the expiration date was approaching or past – the system would send out a special alert to the employee.
Chemical Disposal
Utilizing both the RFID enabled handheld reader, as well as the mobile cart, chemical disposal stations were setup. These stations were used to confirm each chemical that was either completely used or disposed of due to underlying issues. The process to run chemical disposals was very similar to conducting an inventory. The tags on the disposed chemical containers were read and the information was sent to the pharmaceutical company’s main software system to mark the chemicals in the system as ‘disposed’.
Summary:
Even though barcode has become a mainstay within life science companies, the use of RFID technology can make processes run much more smoothly and efficiently. As demonstrated with the pharmaceutical company in this summary, RFID drastically reduced inventory time and greatly increased accuracy over the previously used barcode methods.